CATIA
CFD Estimation of Heat Transfer in Copper Tube for Heat Exchanger using Passive Heat Transfer Augumentation Technique
Sankarsan Mohanty
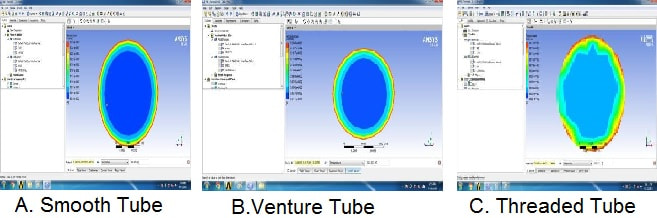
Heat exchanger has been a part of many works producing devices such as air conditioner, refrigerator, automotive, manufacturing, thermal power plants etc. Convective heat transfer is the main phenomena behind the working of heat transfer. A lot of research going on around the world to increase the heat transfer rate of a heat exchanger. One way of increasing this is by introducing extended surfaces inside the fluid flow which will result in more surface area and flow velocity. This technique is known as passive heat transfer augmentation technique. In this project, you will work on increasing the coefficient of convective heat transfer inside a Copper tube using the above technique and will observe the benefits of this technique.
Read more..
Looking to build projects on CATIA?:
CATIA Kit will be shipped to you and you can learn and build using tutorials. You can start for free today!
Implementing passive heat transfer augmentation technique means adding extended surfaces inside the heat exchanger. There are enormous benefits of implementing this technique among which few them are listed below,
- Convective heat transfer rate increases because of increase in surface area which is directly in contact with the flow.
- The flow velocity increase due to the reduction of the cross-sectional area, which leads to a decrease in the workload on a pump.
- Introducing extended surface inside a flow makes the flow more turbulent which results in greater convective heat transfer rate.
- Temperature gradient increases.
- Unlike Fin, with less area, more heat transfer rate is achieved.
- It is cost effective in many ways.
There are a lot of significant benefits of this technique. In the present work, you will analyze heat transfer enhancement for fluid flowing through a copper pipe while introducing extended surface inside the flow using Computational Fluid Dynamics (CFD).
Project Description:
- Heat Exchanger: A Heat Exchanger is a mechanical device which transfers heat between two or more fluid. This device is generally used in the refrigerator, power plants, air conditioners etc. to reduce the temperature of the working fluid.
- CFD: Computational Fluid Dynamics (CFD) is the science of predicting fluid flow, heat and mass transfer, chemical reactions, and related phenomena using numerical methods. It produces a fairly accurate result with ease and convenience. You will use Ansys software for CFD analysis purpose.
Latest projects on CATIA
Want to develop practical skills on CATIA? Checkout our latest projects and start learning for free
Project Implementation:
- At first prepare three CAD model of copper tube with the following specification,
- Smooth copper tube of 1000mm length, 25mm internal diameter and 38mm of outer diameter.
- Internally threaded copper tube of 1000mm length, 25mm internal diameter, 38mm of the outer diameter and 4mm pitch length.
- Venture shaped copper tube of 1000mm where the length of converging and diverging part is 350mm and throat length is 300mm having a 20mm internal diameter. The outer and inner diameter of the pipe is 38mm and 25 mm respectively on both sides. The inner diameter keeps reducing to 20mm until it reaches the throat.
- After preparing the CAD model import it in AcuSolve and perform CFD simulation at steady state.
- Take oil as working fluid at 300°C and mass flow rate of 5kg/s. Take the flow to be turbulent and compute the value of Nusselt no., friction factor, thermal enhancement factor, and coefficient of convective heat transfer for all the three models.
- Compare the results you got during CFD simulation by plotting various graphs and observe the benefits of augmented heat transfer technique in the copper tube.
Did you know
Skyfi Labs helps students learn practical skills by building real-world projects.
You can enrol with friends and receive kits at your doorstep
You can learn from experts, build working projects, showcase skills to the world and grab the best jobs.
Get started today!
Project Brief:
After successful completion of the project, you can observe that the internally threaded copper tube will have better performance in terms of heat transfer rate than the other two models.
Software Requirements:
- CATIA: This is one of the popular solid modelling software made by Dassault System. You will use this software to design your machine structure.
- AcuSolve: You will be needing AcuSolve software to perform CFD simulation and visualization of the result.
- Miniplot: Also, you need plotting software such as Miniplot or Uniplot to plot the result data and compare the results.
Kit required to develop CFD Estimation of Heat Transfer in Copper Tube for Heat Exchanger using Passive Heat Transfer Augumentation Technique:
Technologies you will learn by working on CFD Estimation of Heat Transfer in Copper Tube for Heat Exchanger using Passive Heat Transfer Augumentation Technique:
CFD Estimation of Heat Transfer using Passive Heat Transfer Augumentation Technique
Skyfi Labs
•
Published:
2018-10-16 •
Last Updated:
2021-03-04