ANSYS
Composite bonded patch for fuselage panel
Gurudutt
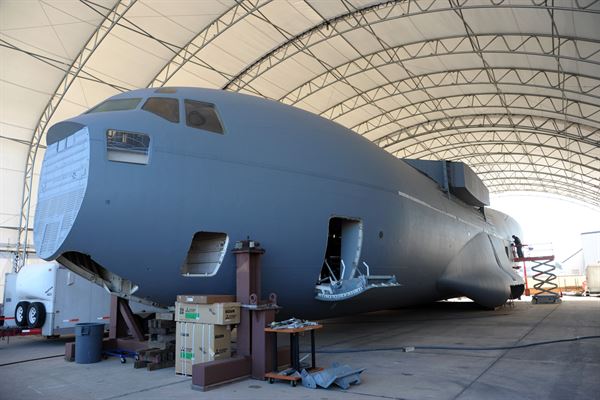
Fiber-reinforced polymer composite is the preferred material for the construction of aircraft and spacecraft. Even used as structural materials for the development of fuselage and due to its applications in the various field, it is used as a primary source for designing aircraft.
Aircraft safety is improving by analyzing the defects in the fuselage and catastrophic failure investigations on aircraft structural components. The primary cause of failure identification and the analysis enable recommendations for corrective action.
Read more..
Looking to build projects on ANSYS?:
ANSYS Kit will be shipped to you and you can learn and build using tutorials. You can start for free today!
Project Description:
- Carbon Fiber: Carbon Fiber made up of carbon crystals aligned in a longitudinal axis. These crystals have long and flattened ribbons such that they form a closed structure. In turn, these ribbons also align in the respective axis with themselves within fibers. These fibers (containing flat ribbons of carbon crystals) in turn bundled by the manufacturer in a bunch of fibers and are woven into carbon cloth, made into a bent and swirled.
- Adhesive: The fiber composites are bonded to themselves and numerous different substrates, with the help of cutting-edge adhesive formulation. These adhesives are available in the form of liquids, pastes and also as films for composite bonding. It provides the maximum strength, stability, and resistance on the exposure to high temperature.
- Epoxy: When two or more objects with the different properties have to adhere to each other for a long duration, the best way to accomplish that is with epoxy
Latest projects on ANSYS
Want to develop practical skills on ANSYS? Checkout our latest projects and start learning for free
- Parameters for calculation of composite Panel
- Ultimate tensile strength = 1600Mpa
- Density = 1800 kg/m3
- Poisson’s ratio = 0.75
- Elongation = 1.6%
- Factor of safety = 1.5
- Cross sectional area A = 200*2 = 400 mm2
- Parameters for calculation of composite strip
- Ultimate tensile strength = 377 Mpa
- Tensile modulus E = 799 Mpa
- Density = 1800 kg/m3
- Poisson’s ratio = 0.75
- Factor of safety = 1.5
- Cross sectional area A = 25*2 = 50 mm2
Did you know
Skyfi Labs helps students learn practical skills by building real-world projects.
You can enrol with friends and receive kits at your doorstep
You can learn from experts, build working projects, showcase skills to the world and grab the best jobs.
Get started today!
Methodology:
- Material selection is done based on the need.
- Evaluate the damage and find the repair technique
- 3D modeling of the composite panel is done.
- Apply the boundary conditions for analysis
- An analysis of the repaired panel is done.
- Fabrication and testing of best repair technique
- Comparison of results and validation
Future Work:
The future works that can be done in this project are:
- Compressive test for the various aerodynamic loading
- Bending test for the various aerodynamic loading.
This project is on carbon composite but in the future, it can be carried on aramid and glass fiber also.
Kit required to develop Composite bonded patch for fuselage panel:
Technologies you will learn by working on Composite bonded patch for fuselage panel:
Composite bonded patch for fuselage panel
Skyfi Labs
•
Published:
2019-07-30 •
Last Updated:
2021-05-14