Mechanical
Glass Hybrid Fibres Epoxy Composite Material using Hand Layup Method
Sankarsan Mohanty
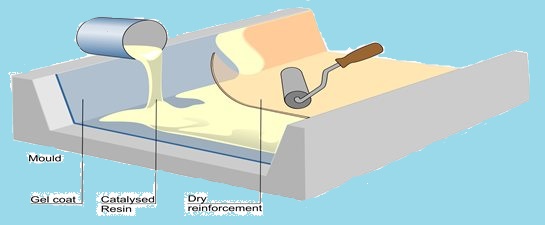
Usage of heavier materials in various fields has led to a lot of fuel consumption. It has been a challenge for material engineers to come up with designs and materials that are lighter and yet better in terms of physical characteristics. This has called for researches into material development for the production of lighter materials of the same or even superior mechanical properties to the existing materials in this area of applications. This project work is dedicated to the study of the mechanical behavior of glass and epoxy composite materials through physical experimentation like tensile, compression, impact and flexural test to understand the composite behavior on a pin on disk machine.
Read more..
Looking to build projects on Mechanical?:
Mechanical Kit will be shipped to you and you can learn and build using tutorials. You can start for free today!
This project involves fabricating Glass hybrid composite material. This composite material you need to fabricate using hand layup method as it is easy and convenient to use. Hand layup method is an art rather than a technique as it requires more involvement of human. So, while fabricating you need to be more careful, so that materials will be equally distributed over the volume. This will directly help in achieving good mechanical properties. To know the various properties of your composite, test your composite by various destructive testing methods such as Tensile test and Compressive test using Universal Testing Machine, Impact test using Charpy impact test Machine and wear testing using Pin-on-disc wear tester.
Project Description:
- Composite Material: Materials like Iron, Steel are better in tension but poor in compression, similarly Wood, Cast Iron is better in compression but poor in tension. To gain the benefit of having more such properties in one material we combine two or more materials in some arrangement. These types of materials are called composite materials.
- Fibre Reinforced Composites: Fibre reinforced composites have been widely successful in hundreds of applications where there was a need for high strength materials. There are thousands of custom formulations which offer FRPs a wide variety of tensile and flexural strengths. When compared with traditional materials such as metals, the combination of high strength and lower weight has made FRC an extremely popular choice for improving a product’s design and performance.
- Epoxy Resin: The term epoxy has been widely adopted for many uses beyond fiber reinforced polymer composites. Today, epoxy adhesives are sold in local hardware stores, and epoxy resin is used as the binder in countertops or coatings for floors. The myriad of uses for epoxy continues to expand, and variates of epoxies are constantly being developed to fit the industries and products they are used in.
- Hand Layup Method: Hand lay-up is an open molding method suitable for making a wide variety of composites products from very small to very large. It is the simplest composites molding method, offering low-cost tooling, simple processing, and a wide range of part sizes. Design changes are readily made. There is a minimum investment in equipment. With skilled operators, good production rates and consistent quality are obtainable.
Did you know
Skyfi Labs helps students learn practical skills by building real-world projects.
You can enrol with friends and receive kits at your doorstep
You can learn from experts, build working projects, showcase skills to the world and grab the best jobs.
Get started today!
Project Implementation:
- At 1st create a square box with one side open, using wood with dimension 50*50 mm. This box will be used as a mold for fabricating your composite.
- Then use release gel and spray it over the mold surface to avoid the sticking of polymer to the surface.
- To get a better surface finish in the final product use thin plastic sheets at the top and bottom of the mold plate.
- You need to add reinforcement in the form of woven mats or chopped strand mats. Cut that material as per the mold size and place it over the surface of the mold after Perspex sheet. Then mix thermosetting polymer in liquid form thoroughly in suitable proportion with a prescribed hardener (curing agent) and pour it onto the surface of the mat which is already placed in the mold and make sure the amount of hardener should be around 5% of the resin used. The polymer should be uniformly spread with the help of a brush.
- Then add the second layer of mat on the polymer surface and move a roller with a mild pressure on the mat-polymer layer to remove any air trapped as well as the excess polymer present.
- Then repeat the same process for each layer of polymer and mat, until the required layers were stacked.
- After that place the plastic sheet over the top mold. Don’t forget to spray release gel on the inner surface of the top mold plate. Then keep it on the stacked layers and then apply pressure for a compact material.
- Cure the mold in the room temperature and curing process is done take out the composite out of the mold.
- Then make a few sample specimens for performing the various test. At least Make 3 standard specimen for each test.
- Perform a tensile test using an ATM machine to find ultimate tensile strength, breaking strength, maximum elongation, and reduction in area. From these measurements determine Young's modulus, Poisson's ratio, yield strength, and strain-hardening characteristics.
- Then perform the compressive test in the same machine to find out ultimate compressive strength, breaking strength etc.
- After that perform the Flexural test, Impact test and wear test on the composite material with the standard specimen and note down respective results.
- Compare your results with respect to the different specimen to realize how good your composite in different loading condition.
Project Brief: The composite which you will build most be strong in both compression, tension and bending too. Proper distribution of reinforcements and polymers over the entire volume will result in higher mechanical strength of the composite.
Hardware Requirements:
- Universal Testing Machine: A universal testing machine is generally used to test the tensile stress and compressive strength of materials. It is able to perform many standard tensile and compression tests on materials, components, and structures, it is named as Universal Testing Machine (UTM). You need this machine to perform the various test on the fabricated composite material of yours.
- Charpy Impact Test Machine: The Charpy impact test, also known as the Charpy V-notch test, is a standardized high strain-rate test which determines the amount of energy absorbed by a material during fracture. This machine you will use for the above purpose only.
- Pin-On-Disc Wear Tester: Pin-on-disc wear testing is a method of characterizing the coefficient of friction, frictional force and rate of wear between two materials. As a particularly versatile method for testing wear resistance. You are going to measure frictional force and other parameter related to friction using this machine.
- Flexural Testing Machine: These machines are used to test the flexural strength of a beam. Flexural strength is nothing but the banding strength of a beam under normal loading.
Software requirements:
- Miniplot: You can use this software for plotting and comparing your result data.
Latest projects on Mechanical
Want to develop practical skills on Mechanical? Checkout our latest projects and start learning for free
Kit required to develop Glass Hybrid Fibres Epoxy Composite Material using Hand Layup Method:
Technologies you will learn by working on Glass Hybrid Fibres Epoxy Composite Material using Hand Layup Method:
Glass Hybrid Fibres Epoxy Composite Material using Hand Layup Method
Skyfi Labs
•
Published:
2018-08-27 •
Last Updated:
2021-06-14